New Battery Innovation Centre opened by AVL.
- Thomas Fone
- Sep 23, 2021
- 2 min read
AVL List has opened a brand new Battery Innovation Center, the company says it marks the addition of a crucial future platform to the AVL portfolio. The 1,600-m² facility takes its place at the company’s headquarters in Graz. It will support AVL projects and developments globally. In launching the new centre, the engineering service provider applies the principle and expands the scope of simultaneous engineering.

The company says at the AVL Battery Innovation Center, functional battery development is closely linked with the expertise of production planners and input from parts and machine manufacturers. The aim is that batteries developed by AVL will display a far higher degree of maturity across all phases of development. Furthermore, the company will see an improved process through to market maturity that will be significantly quicker, as function, manufacturability and costs can be balanced and optimized early. Overall the reliability of the validation will ensure consistently high quality.
All the current core processes of module and pack production can be mapped at the various stations, some fully automated. Thus, regardless of cell type, target voltage and integration level, it will be possible to reproduce all the steps involved in module construction and, in the future, pack construction. Furthermore, the industrial robots in the BIC enable AVL to meet requirements in the areas of Cell-to-Body and Module-to-Chassis, which are increasingly crucial for automobile manufacturers.

The improvement of production processes is accompanied by advanced Virtual Reality (VR) methods. In addition, augmented Reality (AR) is increasingly used in the field of assembly processes. AVL says it is now possible to develop products parallel to the industrialization of batteries, to a degree previously unattained.
The company will offer validation of manufacturing technologies in real large-scale production conditions. As a result, the production processes designed can be tested thoroughly in real conditions in the pilot line. AVL says this makes it possible to industrially process all the cell types currently available on the market, with sizes right up to Cell-to-Pack dimensions. Furthermore, batteries – ranging from individual A-sample production to batches of several hundred batteries – can also be manufactured in the BIC, whilst comprehensively monitoring defined quality characteristics.
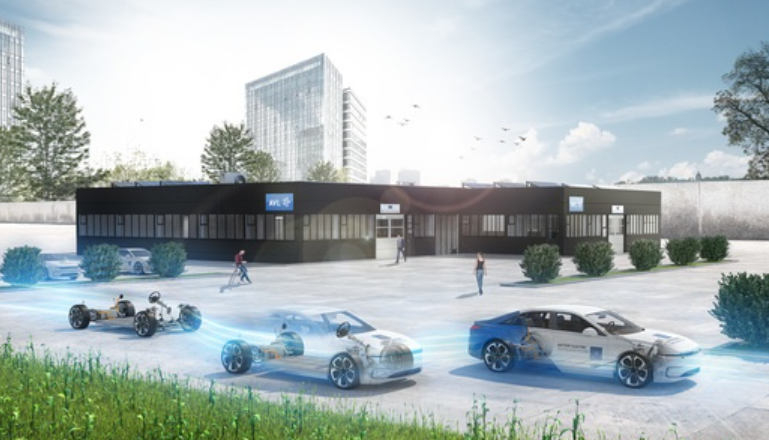
Work on the AVL Battery Innovation Center in Graz began in 2018. The project is being supported by the Austrian Research Promotion Agency (FFG) and the European innovation programme Important Projects of Common European Interest (IPCEI). Prof. Helmut List, Chairman and CEO of AVL List GmbH: “The technology for affordable high-voltage batteries for electric cars, which are suitable for customer use, is already very advanced. In contrast, there is still a lot of potential when it comes to production. We are addressing this with our Battery Innovation Center, as optimizing production procedures is a key factor on the road to e-mobility. We started to rethink assembly processes over five years ago radically. With the BIC in Graz, we are now offering our customers an innovative center for all modern battery development needs.”
Comments