
Mercedes-Benz has started producing high-performance batteries for its all-electric luxury EQS at its Stuttgart-Hedelfingen plant, ahead of the sedan's world premiere on April 15, 2021. The EQS marks the start of a new generation of high-performance electric vehicles and will offer a range of more than 700 km (based on WLTP), based on a high-efficiency powertrain and advances in battery energy density. Having integrated battery production seamlessly alongside existing transmission production, the Hedelfingen plant is an integral part of Daimler's global battery production network. The quick ramp-up of its global battery production capacities and targeted expansion of battery competencies through the entire value chain are the key pillars of the Mercedes-Benz electric initiative - from basic research, cell production up to batteries' afterlife, including 2nd-life applications and recycling.
This in-house know-how and vertical integration are critical for playing a leading role in electric vehicles. In addition to scaling up the EQS battery production, the Mercedes-Benz Drive Systems Campus Untertürkheim will specifically expand its research and development activities in the field of e-mobility - through campus for electric and electrified drive systems- as announced earlier this month.

"The roll-out of our electric initiative is accelerating as we pursue CO2-neutrality. Our next all-electric model - the luxury sedan EQS - built on a dedicated electric platform is already in the starting blocks. Therefore, the start of production of its high-performance battery systems in our plant in Stuttgart-Hedelfingen is an important milestone.
As part of the transformation of our company and our products, we are significantly expanding our battery competencies across the entire value chain. Thereby we continue to make efforts to help the next generation of batteries achieve a breakthrough even faster."
Markus Schäfer, Responsible for Daimler Group Research and Mercedes-Benz Cars COO.
The Hedelfingen plant, as part of the Mercedes-Benz Untertürkheim location (Germany), is responsible for the production of battery systems for the Mercedes-Benz EQS, as well as the upcoming EQE. The plant has a production and logistics area of about 16,500 m², relying on state-of-the-art systems, including a wide range of Industry 4.0 technologies. The highly complex lithium-ion battery system is produced on an approximately 300-meter production line with more than 70 production stations and a high number of automated and manual steps. A variety of components, including up to 12 cell modules and the so-called EE-compartment for the intelligent integration of power electronics, make up the EQS battery system.
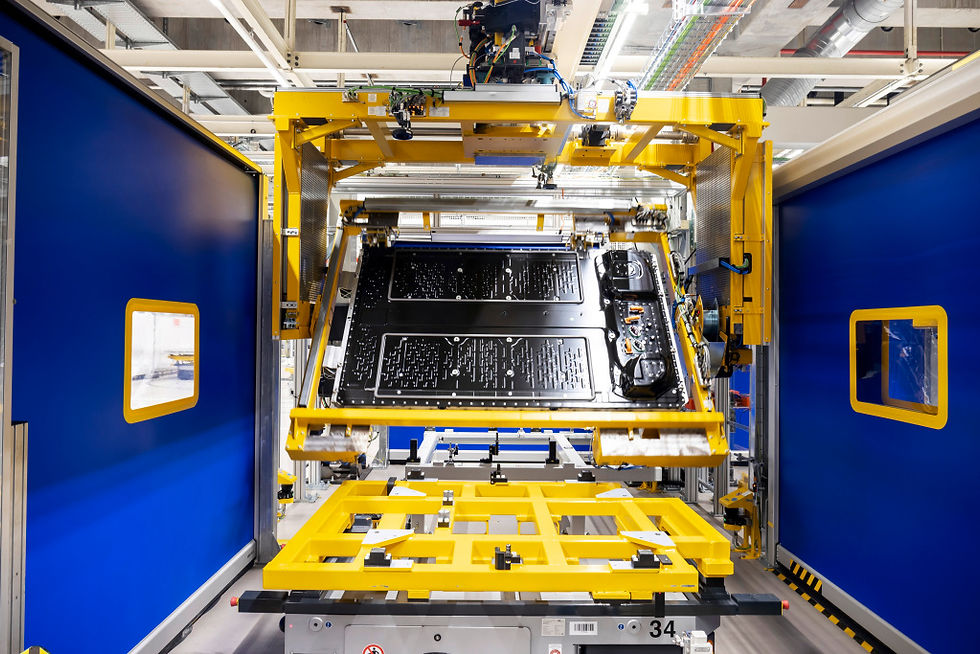
The Mercedes-Benz Berlin site assembles the EE-compartment. The EQS will be equipped with battery layouts enabling different range and performance variants. With an installed energy content of up to 108 kWh, the EQS targets, according to WLTP, a range of more than 700 kilometres, aided by best-in-class aerodynamics. The in-house-developed software technologically enables updates over the air (OTA), ensuring that the energy management of the EQS will remain up-to-date over the entire lifetime of the vehicle. Besides its CO2-neutrally produced cells, the EQS battery cell chemistry includes nickel, cobalt and manganese in a ratio of 8: 1: 1, cutting the cobalt content to around ten percent.
The EQS is produced alongside the new S-Class at the "Factory 56" in the Sindelfingen plant. The site operates CO2-neutrally from the beginning. As early as 2022, the company's own Mercedes-Benz passenger car and van plants worldwide and the Hedelfingen plant will also use CO2-neutrally.

With the bundling and extension of its battery activities at the Mercedes-Benz Drive Systems Campus at the Untertürkheim site (Germany), the company strengthens its expertise in the field of e-mobility.
Research and development activities present at the location include the e-technology centre and cell technology centre. Prototypes for the electric drive system are built, and cell technologies are researched and tested.
To deepen its competence as a centre for battery technology, a new factory for the small-series production of future lithium-ion battery cells is being planned, starting its operations in 2023. The sustainability factor, transparent cell development through to recyclability, plays a significant role in this. The focus on in-house know-how and high vertical integration is critical for a leading role in electric vehicles. Mercedes-Benz plans to invest a three-digit million amount in the transformation of the site.
Comentarios