Holistic Vehicle Development for Future Trucks
- Thomas Fone
- Aug 20, 2021
- 3 min read
New regulations to limit CO2 emissions from newly manufactured heavy-duty vehicles will pose challenges for OEMs. However, German Engineering firm FEV says it offers many solutions to allow commercial vehicle manufacturers to meet the new obligations. They say they can provide advanced powertrain and propulsion systems and other innovations such as bespoke aerodynamic approaches and predictive vehicle controls based on various parameters such as commercial vehicle routes.
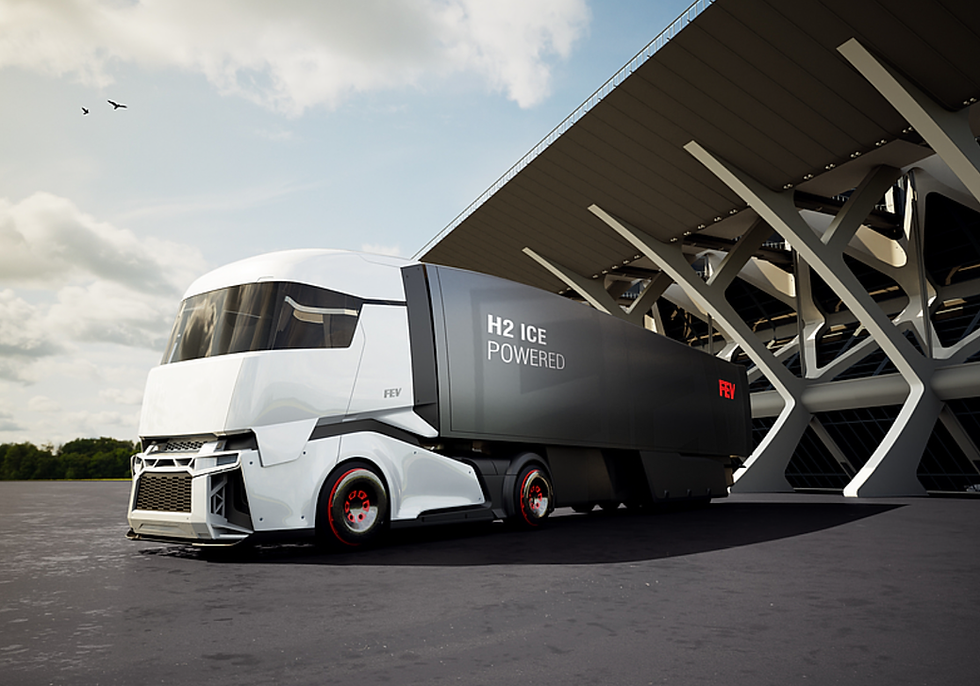
Regardless of the type of drive, future trucks will be characterised by predictive control concepts based on vehicle networking. Accordingly, FEV is developing real-time driving style solutions by collecting and evaluating parameters and infrastructure data via 4G/5G mobile networks. The aim is to achieve maximum efficiency and minimising operating costs for customers. Typical information that flows into the algorithms includes vehicle position, traffic signs, traffic light timing, and rate information from charging stations on planned and alternative routes. In addition, information on the number of road users and their behaviour.
"By combining targeted navigation with assessed energy use, such as driving modes, routes for recuperation, or recharging at the charging point, the average range of commercial vehicles can be increased by double-digit percentage points. Sub-functions such as online estimation of actual vehicle mass and measurement of individual driving style also enable the prediction algorithms to be highly precise," said Professor Stefan Pischinger, CEO of FEV Group. "In the future, it will become quite natural to include not only driving and resting times, but also the recharging time in logistics and route planning."
FEV points out that by leveraging many years of simulation experience, especially in computational fluid dynamics (CFD), the company can utilise aerodynamics benefits for its customers. A prime example is Battery electric trucks, which require a less frontal area for cooling and allow for increased cabin area thanks to reduced dimensional constraints. As a result, reductions in drag as significant as ten percent can be achieved, resulting in decreased energy consumption and increased range.
On the drive side, future trucks will be battery-electric, powered by a fuel cell, or powered by a hydrogen combustion engine. Commercial vehicles are explicitly developed for specific usage and depending on the area of application, new development requirements will emerge in addition to normal vehicle development.
"Our customers appreciate the holistic vehicle development from a single source and the associated time and cost advantages, especially when it comes to meeting new emission requirements," said Professor Pischinger. "FEV has the expertise and resources to bundle its competencies across disciplines in order to deliver the optimal sustainable vehicle solution in accordance with the customer's interest."
FEV offers an example of battery-electric trucks, typically customers are concerned with performance and range. FEV aims to address these requirements with its scalable modular battery system that integrates existing and homologated batteries from the passenger car segment. FEV also developed a gateway solution for the battery management system (BMS) to coordinate the individual batteries within this framework. The company says that this approach can significantly reduce its customers' time-to-market. In addition, the development services provider is working on new Cell-to-Pack packaging concepts that allow for higher energy density at the battery level, thus increasing the long-distance suitability of commercial vehicles where needed.
Various electric drive solutions are offered. Depending on the vehicle and customer requirements, either centrally arranged drive units combined with conventional axles or axles with an integrated electric motor and transmission are used. In many cases these electric drives also involve multi-gear transmissions. For these instances, the company has developed dog clutch and electro-mechanical actuation systems specially optimised for this purpose. FEV says the advantage lies in their high efficiency and extraordinarily flexible application, since neither pneumatic nor hydraulic auxiliary energy is required from the vehicle. The technology is successfully used, for example, in an automated 3-speed transmission for heavy trucks with a weight capacity of up to 90 tons in mining applications.
The intelligent interconnection of different circuits at different temperature levels can significantly energy savings in electric trucks. Examples include using waste heat from the battery or the electric motor via a heat pump to condition the cabin, which can increase both range and driver comfort.
Comments