Cloud-based software, Intelligent Robotics and AI to be deployed as Volkswagen Launches Digital Push
- Natalia Sousa
- Aug 10, 2021
- 2 min read
Updated: Feb 28
Volkswagen says it has launched a digital transformation push across its plants in the United States and Mexico. All part of an estimated $1 billion investment in electric mobility and digitalization that the company will undertake in North America up to 2025. The company is bringing cloud-based industrial software, intelligent robotics and artificial intelligence into factory operations. As a result, the company aims to drive a 30 percent increase in manufacturing performance for its electric vehicle assembly and large-scale car assembly in Chattanooga, TN, and Puebla, Mexico. In addition, a training program has been announced alongside to accelerate its digital push.
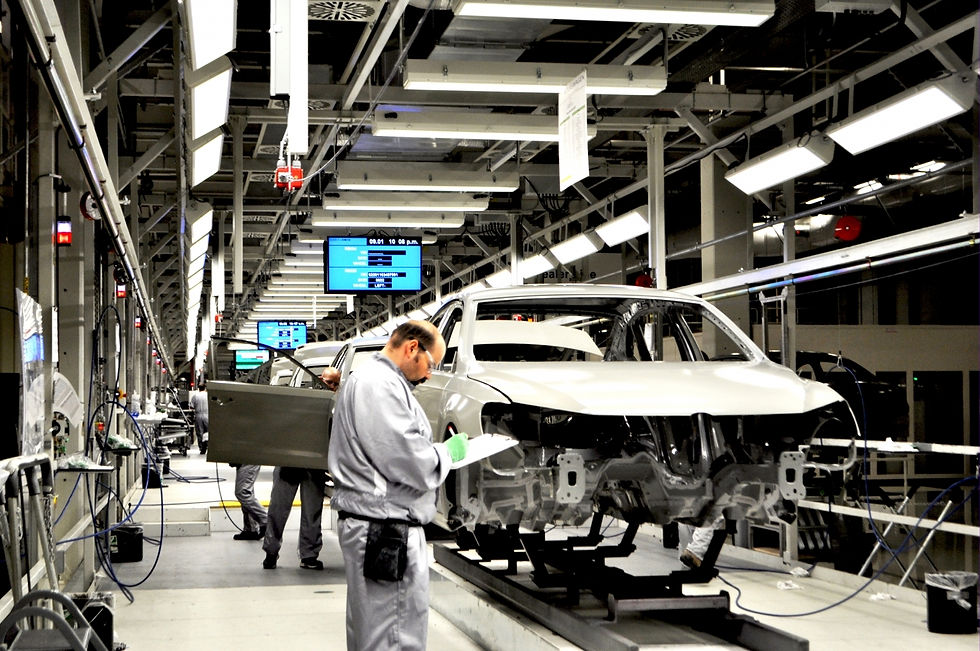
"We're pushing our ambitious digital transformation to make Volkswagen's factories in the North American region more productive, connected and more sustainable than ever before", said Johan de Nysschen, chief operating officer at Volkswagen Group of America. "Our digital transformation also supports skilled labour and high-profile, future-proof jobs throughout North America at our sites in Chattanooga, Puebla and Silao."
The company says that the unified launch of the software, AI, and robotics could allow Volkswagen to optimize collaboration and enhance its employees and suppliers' overall assembly process and workplace environment. Volkswagen's ultimate aim is a more efficient system, including managing material flows, optimizing machines and procedures, and increased savings in energy consumption for manufacturing-related processes.
Volkswagen Group's cloud-based IT platform expects to boost global manufacturing performance by sharing data connections, real-time information and software apps for industrial machinery from all connected Volkswagen and supplier facilities. Twenty-one global Volkswagen Group plants and 13 global suppliers have already joined this global IT platform. In addition, north American regional suppliers are encouraged to participate.
Volkswagen's North American sites are already preparing to deploy software applications from the Industrial Cloud. For example, an intelligent conveyor motor monitoring app could help reducing downtime and supports predictive maintenance technologies. Another example is cameras with machine vision technology that quality-check engine components. In addition, Volkswagen teams are working on more than 50 projects, spanning from shop floor management to quality assurance and logistics within the factory.

Volkswagen has deployed collaborative robots (cobots) to support its workforce over the past several months. These cobots perform final inspection checks and measure for gap precision. For example, on the Tiguan line in Puebla, a cobot measures 26 checkpoints in less than a minute − the first application of this technology in the global Volkswagen Group. It is also expected to assist with spot-checking welding patterns when the ID.4 electric SUV begins assembly in Chattanooga in 2022 – an enhancement that will further support Volkswagen quality standards in manufacturing.
A new artificial intelligence tool, developed in-house at Volkswagen's AI Detroit center, will help supervisors manage factory schedules in Chattanooga. This type of technology is designed to reduce the amount of time supervisors spend balancing inputs like training levels, time off and other factors. The AI scheduler can analyze all key variables and provide suggested schedules within minutes of a request.
"We need a production network that is just as advanced as our future vehicles for North American customers," said Susanne Lehmann, Senior Director Production, Volkswagen de México. "Through our work we already see not only the value of what's been implemented, but the promise of what's to come."
Comments