Behind the Scenes. Volkswagen Brazil's Test facilities, and 50 years of local Testing and R&D.
- Natalia Sousa
- Dec 3, 2021
- 4 min read
Updated: Feb 28
The vehicle safety laboratory of Volkswagen do Brasil celebrates its 50th birthday. In Brazil, the company, an early pioneer of vehicle safety and crash tests, Volkswagen implemented its Vehicle Safety Laboratory 50 years ago, something unprecedented in the country. Since 1971, the laboratory has been integrated into the Product Research and Development area, working to create and design new models and improve vehicles in production.

Volkswagen do Brasil's Vehicle Safety Laboratory is a pioneer in Latin America and a reference in the VW Group, being one of the most modern, advanced and equipped of the company in the world for the development of vehicles capable of offering the maximum performance in safety. In the early 1970s, crash tests were the primary tool for evaluating and developing car safety items. Apart from active safety items, such as brakes, suspension and tires, the attention of technicians at the time was already focused on passive safety: mitigating the consequences of accidents.
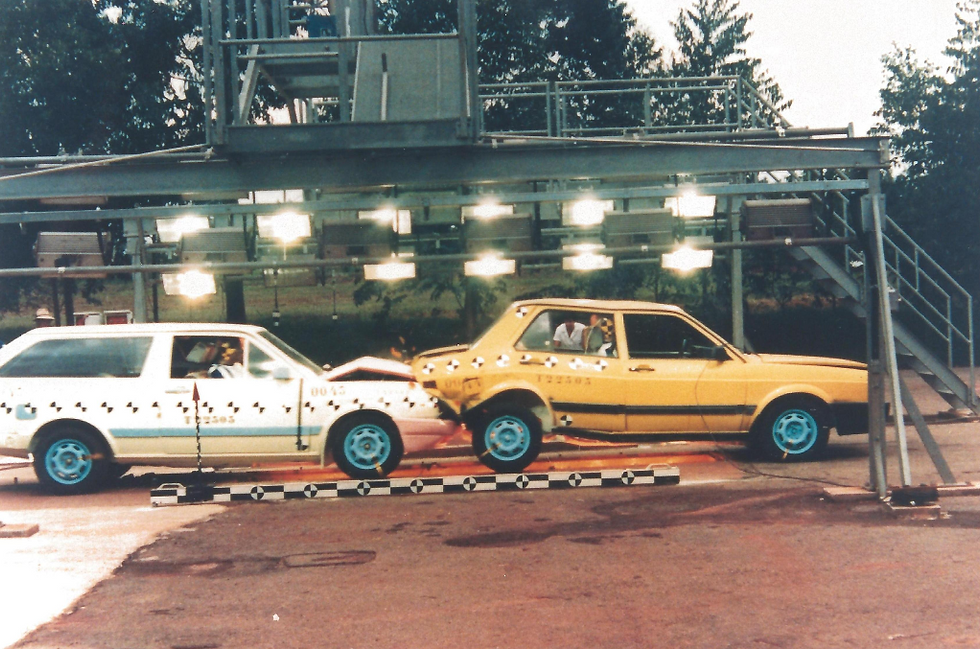
The tests were not limited to the study of body deformations and impacts caused on dummies (dummy simulating occupants of the vehicles tested). An essential item was the integrity of the fuel system, which could not admit leaks. In addition, other components of the car were individually tested, such as seat attachments, door locks and seat belt locks.
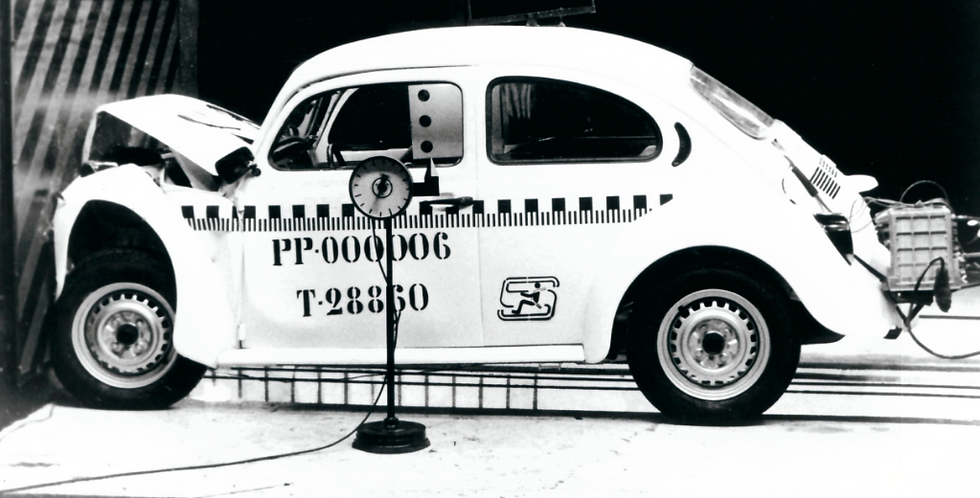
Volkswagen also has other pioneering actions in vehicle safety. It was the first automaker in Brazil to develop front airbags and use ABS brakes.
In 1970, the Vehicle Safety Engineering department was created and the first laboratory was inaugurated the following year at Volkswagen's facilities in the Ipiranga district, in São Paulo (SP). In the beginning, frontal and rear collision tests were carried out. At the same time Volkswagen's product line introduced major innovations, such as the VW 1600 TL, a sporty-looking fastback sedan; the 1500 version of the Fusca, soon dubbed the Fuscão, and the Variant van. Another newcomer was the Karmann Ghia TC, an exclusively Brazilian version of the sports model inspired by the Porsche 911. The locally produced models required a lot of local safety development work, even those based on cars made in Germany, such as the Variant and the 1600 TL were modified for the Brazilian market. Other exclusive Brazilian models were developed in the following years, such as the SP1 and SP2 sports car, the iconic Brasília, the Variant II, the Gol family, and even the Fox (version of the Voyage/Parati aimed at the USA/Canada).

In the mid-1980s, the Vehicle Safety structure was transferred to the Anchieta factory in São Bernardo do Campo (SP). The inauguration of the new crash test track was in 1989. The new features enabled the development, for example, of the Polo and Fox family, with an emphasis on versions produced for the European market of both vehicles, meeting the strict requirements of European legislation at the time.
With the support of the Vehicle Safety Laboratory, some of the Volkswagen models were developed which achieved top marks in safety in the tests carried out by Latin NCAP, in fact the VW up! was the first compact vehicle produced in Brazil to obtain 5 stars for adult occupant protection. Other Volkswagen soon followed in this feat, the Volkswagen Polo, Virtus, and the T‑Cross. These three models have five stars (maximum grade) for both adult and child protection categories.
The Polo, Virtus, T-Cross, Jetta and Tiguan Allspace models also earned the extra recognition "Advanced Award", given to vehicles that meet pedestrian protection criteria with technologies that mitigate injuries in situations of pedestrians. The Polo was the 1st model sold in Brazil to receive this award.
Volkswagen in Brazil developed locally new vehicles with pedestrian protection technologies. During the development of a new product, VW's Vehicle Safety engineers conduct tests to assess the vehicle's influences on the pedestrian. Then, if necessary, they redesign components (such as bumpers, hood, windshields, and vehicle columns) to mitigate impact injuries without compromising the vehicle's structural integrity.
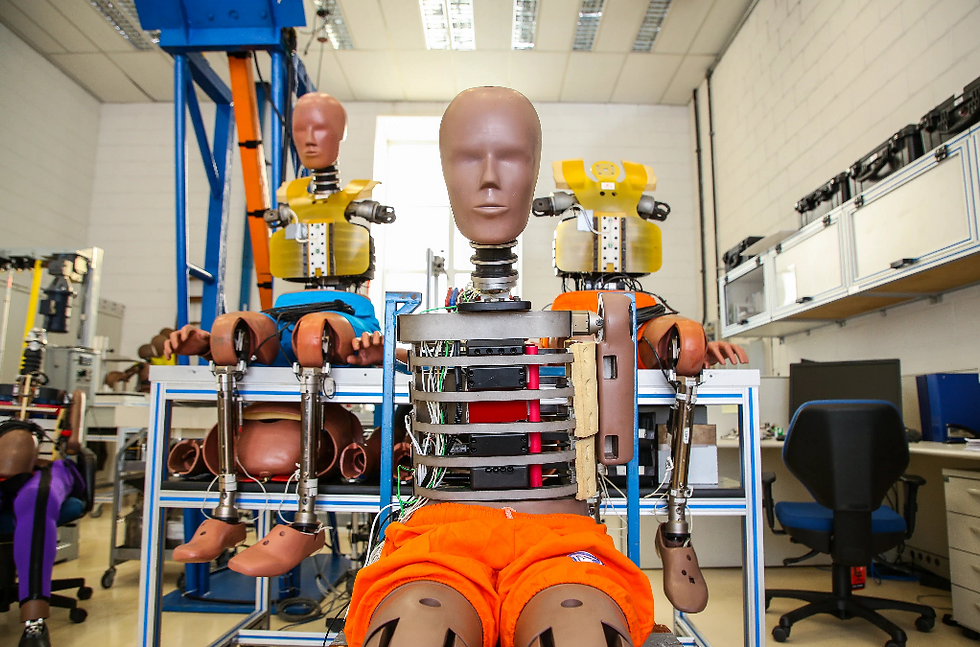
Tests are carried out primarily through virtual reality simulations. Then, they are verified and validated in real-tests with state-of-the-art machines and sensors that simulate the human body, evaluating impacts on the leg, pelvis and head.
Today, active safety and driving assistance systems play an important role in protecting vehicle drivers and passengers and pedestrians. In addition to the traditional tests, carried out for decades, the engineers and technicians at the Vehicle Safety Laboratory are currently working on developing and improving systems based on digitization and data processing. Digital evolution makes it possible for ABS brakes to interact with various sensors, ranging from accelerometers to cameras, radar and ultrasound.
Digitization also makes it possible to carry out virtual tests, which accelerate the development of car components by simulating real situations. Thus, there is a great gain in development time and cost reduction: the car is only subjected to a physical crash test after numerous simulations.
The sled test (sled) evaluates the consequences of a traffic accident for occupants using the vehicle body with high-precision technology. It is the physical simulation of an impact in an intermediate step between virtual assessments, made on a computer, and the crash test of the complete vehicle.
In the Sled test, frontal, rear or side collision tests can be carried out at different speeds and the isolated evaluation of certain components, such as seat belts, airbags, seats, steering column or instrument panel, etc. Volkswagen in Brazil performs several crash tests in the most varied situations during the development of a new vehicle. Different types of barriers and speeds are used in order to cover the greatest number of accident simulations that can occur on passable roads. In addition to the crash test laboratory, the area has climate chambers for analyzing the activation of airbags, traction devices for resistance tests in the bodywork of the anchorage points of belts and seats, denting the roof and door, testing the fuel tank and bumpers.
The "crash test dummy", or anthropometric dummy, is essential for developing a safe vehicle. It is a calibrated test instrument used to measure the potential for full-body injuries in vehicle collisions. With different standard sizes, these anthropometric figures simulate the human response to impacts, accelerations, deflections, forces, and moments generated during an accident.
New requirements arise each year, the company must adhere to both Brazilian legislation and the safety protocols of independent institutes all becoming increasingly strict. The company says 50 years after its inauguration, Volkswagen do Brasil's Vehicle Safety Laboratory continues to fulfill its mission with a focus on developing and producing increasingly modern and safe vehicles.
Comments